Then there are certain achievements that make a working group, a team of designers, a firm of architects and engineers proud. For us at Stancanelli, one of these projects is the Centro del Mediterraneo, a civil and oncological hospital built by Humanitas just outside Catania, in the Misterbianco area. Well-integrated into the rural landscape, among olive and citrus groves, the Centre is at the crossroads of three of the island’s major roads and just 15 minutes from Fontanarossa airport.
The Centro del Mediterraneo was built in record time, just two years: from 2018 to 2020 (it was delivered on 6 April), and was immediately equipped to house intensive care to cope with the Covid-19 emergency in the Catania area.
This is a major achievement, as is the size of the hospital: an area of 200,000 m2 for a covered surface area of 15,000 m2, with a medical supply of 240 beds, for five buildings that crown a large, innovative location specialising in treatment and research (there are in fact plans for teaching rooms and a close collaboration with the University of Catania).
Saving time and resources (manpower and savings); reducing seismic vulnerability, thanks to the adoption of isolators; cutting-edge technical and construction processes – through the use of reinforced mats; modern planimetric design to avoid overlapping flows (patients, medical staff, visitors, goods); integration with the local landscape heritage. These are the issues that our team dealt with during the construction of the Humanitas Hospital Centre, for which it oversaw all the design phases up to the final design, the executive design of the structural works, the construction site and the overall physical construction as lead member of a temporary association of companies, working in synergy with other design and non-design teams.
Below, and in the detail of images and text, are some of the specific features that make the Humanitas Centre one of the works that best describes the innovative drive of the Stancanelli group and the philosophy of our company.
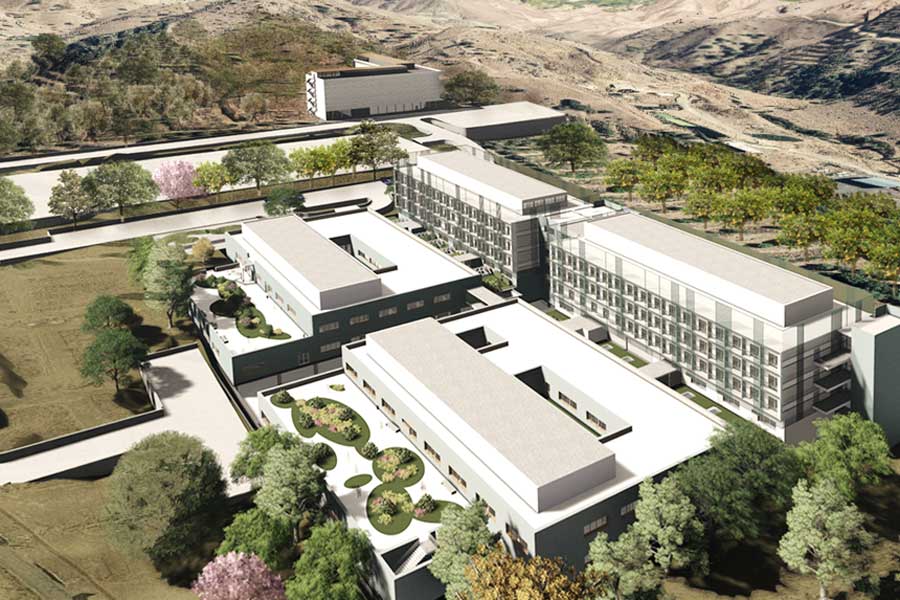
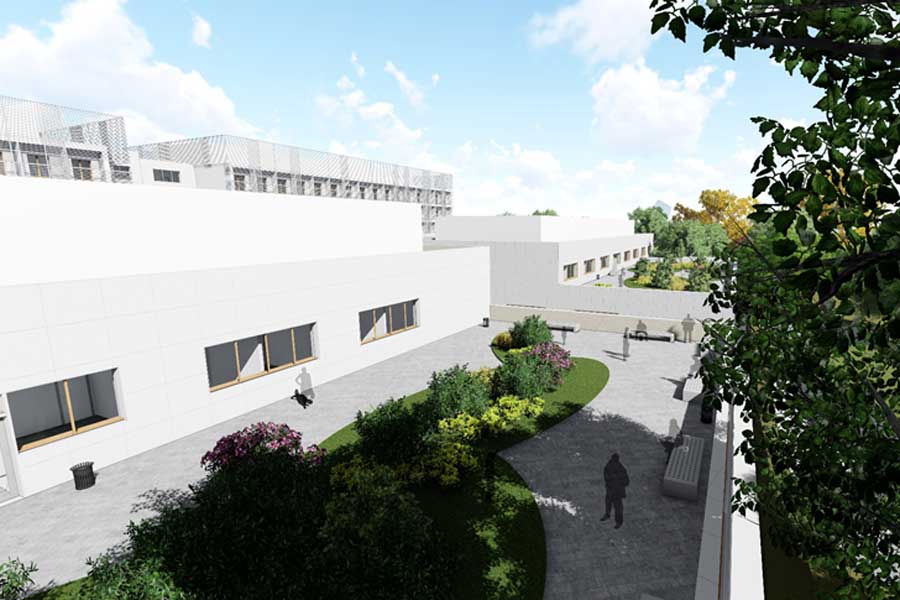
1) ARCHITECTURAL INNOVATION
From a planimetric point of view, the actual hospital occupies the central area of the lot, while the pertinent buildings, which integrate its functions, are arranged around it.
The centre is characterised architecturally by the juxtaposition of simple vertical and horizontal volumes of different shapes and sizes: hospital plates and towers. The hospital towers are built as triple bodies with the services in the centre and the large single and double rooms on the sides, while the operating plates (one built and the other postponed at the client’s request) made it possible to compact the outpatient functions to reduce the number of stretchered paths and increase efficiency and comfort for patients.
The desire to integrate the complex with the landscape (in order to preserve the great heritage of olive and citrus trees already present in the area and subject to landscape restrictions) led us to design buildings that were not extremely high (as is often the case with many hospitals), while also trying to limit land consumption in favour of large gardens. We also wanted to focus on the psychological component of patients, so we sought to bring light and greenery into the building, using large windows, sheds, terraces and patios that penetrate the building, creating a serene and pleasant place, both usable and full of light.
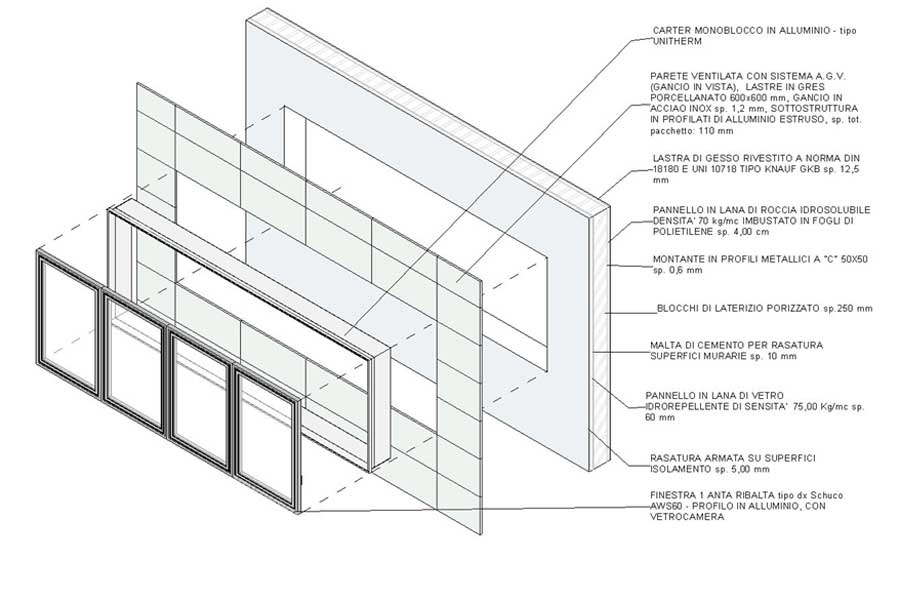
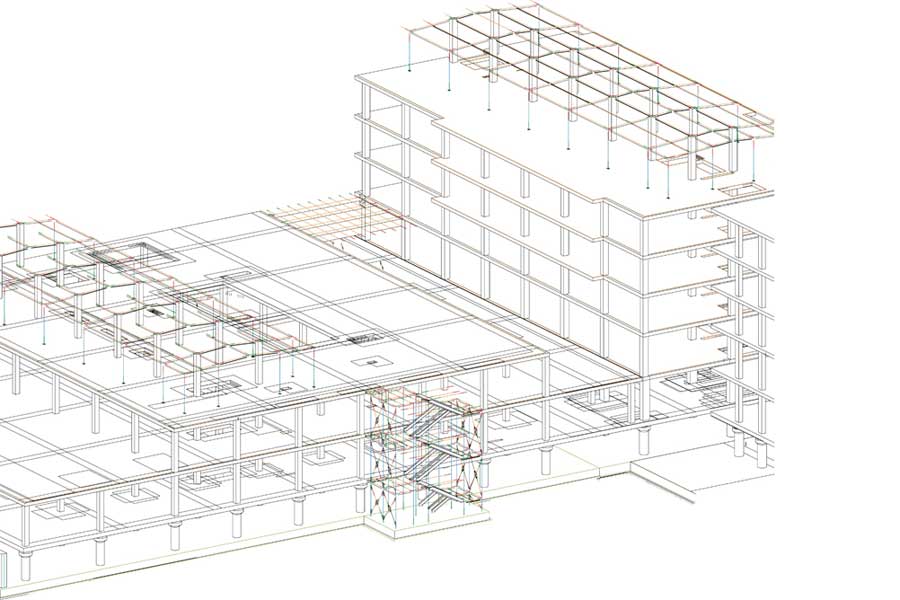
2)TECHNOLOGICAL INNOVATION
The project was entirely built using BIM technology to increase design accuracy, minimise waste and facilitate the construction and future maintenance of the complex. The technology ensured:
– precision on the calculation and forecasting of costs;
– meticulous listing of all the construction materials used in the project (from fixtures to reinforcing bars, from cubic metres of plaster to the plumbing of the radioprotected areas);
– optimisation of the use of materials, reduction of waste;
– planning of material storage and speeding up installation;
– continuous collaboration between the various disciplines (architectural, structural, plant engineering), to manage “in real time” the interferences between the various project levels;
– extremely rapid design and implementation.
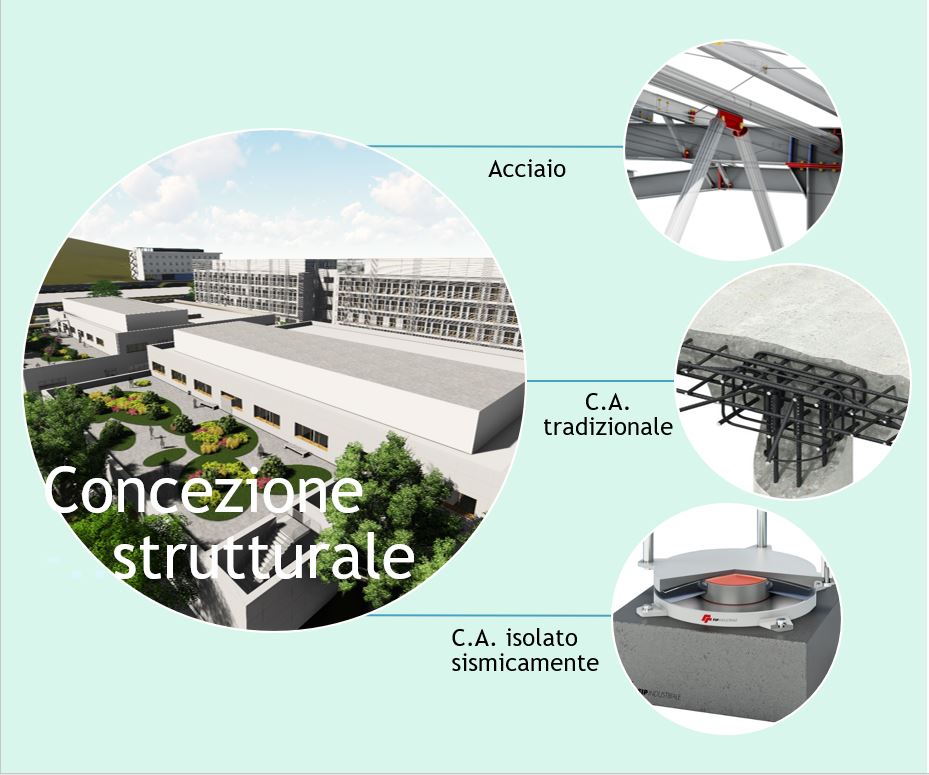
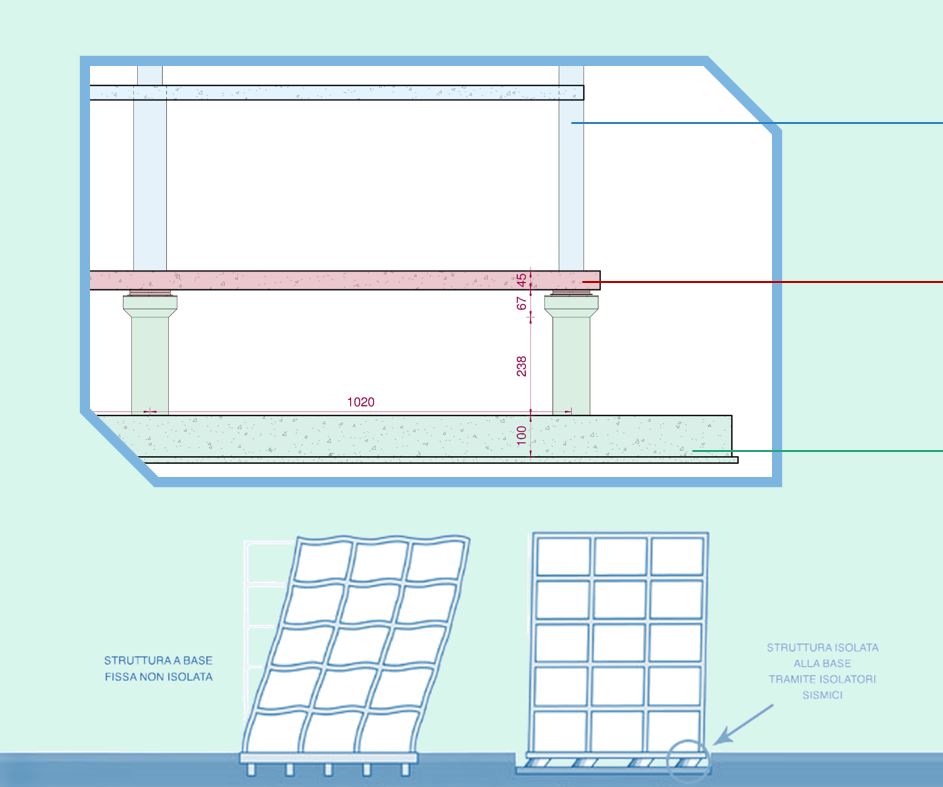
3) STRUCTURAL INNOVATION
Structurally, the choice was made for seismic isolation at the base of the reinforced concrete structure. This is a modern engineering technique with many advantages:
- the structure is slimmer than a traditional reinforced concrete structure with a fixed base, limiting much of the seismic action with the isolation system;
- in the event of an earthquake, deformations are concentrated mainly in the isolation system, so that horizontal stresses and displacements are not very significant, and damage to structures and machinery is avoided: this is a necessary condition for a hospital structure that must guarantee continuous operation;
- The use of insulators also makes it possible to create continuous floors (elastic, quick to build and functional for plant engineering), overcoming the principle of the hierarchy of strengths.
- the cost of the building does not deviate much from that of a traditional structure, as the isolators make it possible to streamline the structures above the isolation floor;
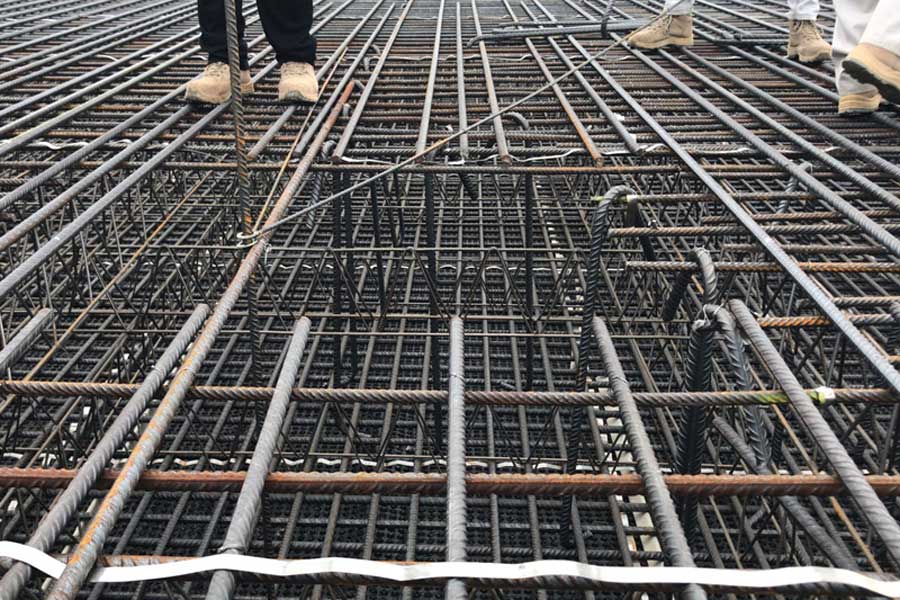
4) CONSTRUCTION SITE INNOVATION
A structure of this size would require the use of thousands of kilometres of reinforcement bars, which would take a very long time to lay, and introduces a heighten risk of inaccuracies or errors. The decision was therefore made to use BAMTEC reinforced mats, with the entire ceiling and wall reinforcement, as well as the circular columns and all the bent reinforcing bars being produced and assembled in the workshop.
An integral part of the construction project was also the study of the compatibility of the installation of these mats with the seismic isolators used below the isolation plane.
The effectiveness of the choice of reinforcement mats is evident from:
– the possibility of industrialising the construction process, quickly and compatibly, such as: continuous slabs, pre-assembled reinforcement, formwork system;
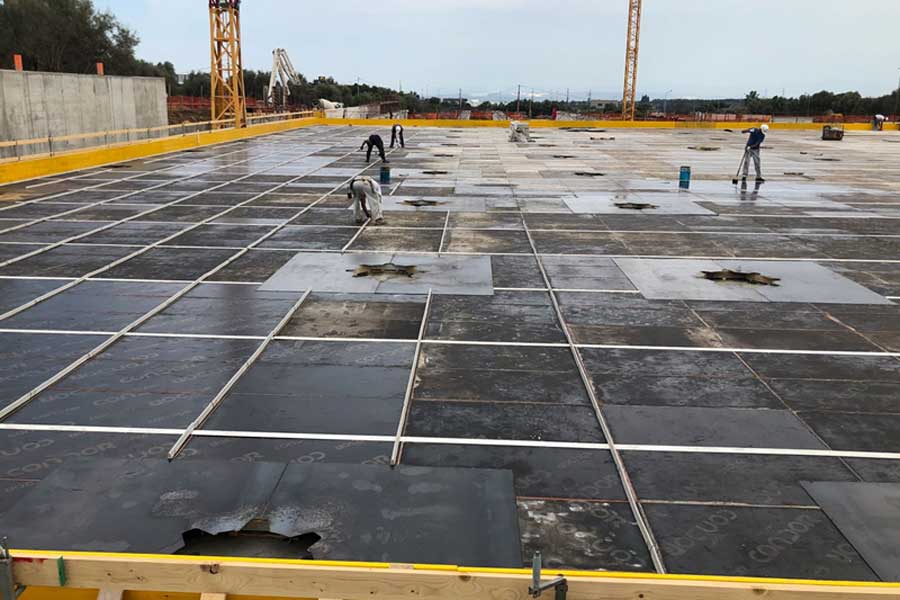
– greater industrialisation of the process, with definite and scheduled times and the guarantee of a review of the boards to reduce accidental errors;
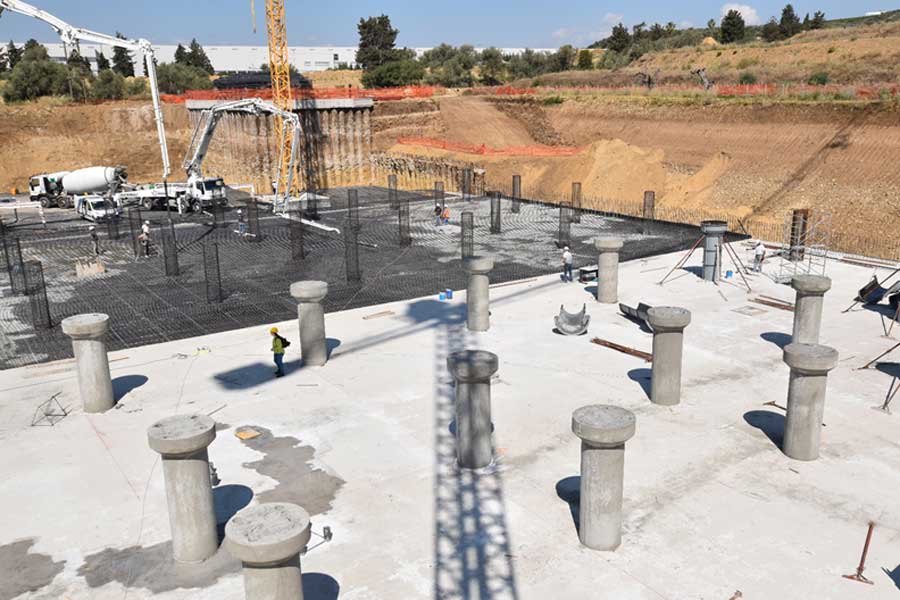
– greater safety for the operators during the cutting of the reinforcement bars; in the transport and handling of the bars to the laying point by crane; in the tying of the reinforcement thanks to the unrolling of the mats;
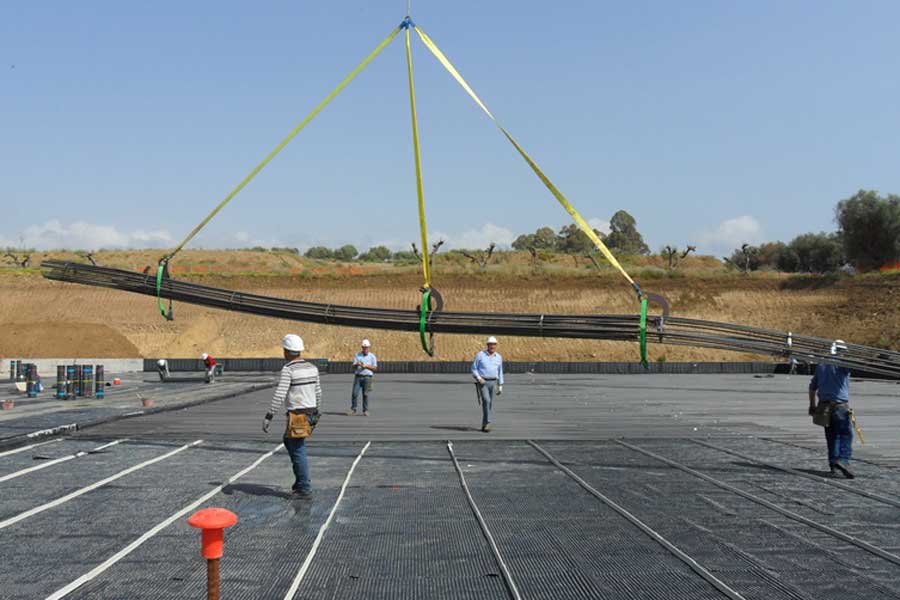
– greater savings in time, labour and costs. Reinforcing a typical 1500 m² slab required almost 2 working days (15 h) of 12 operators, i.e. 180 h in total. The estimated percentage saving is 80% in terms of time and between 25 and 30% in terms of cost.
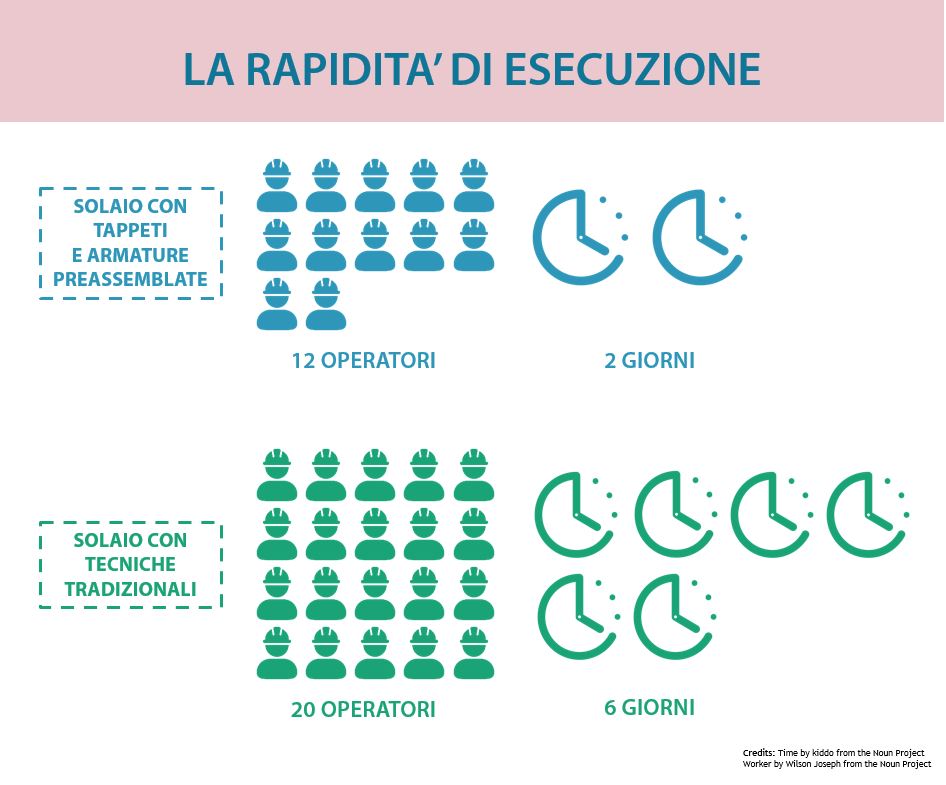